Origin Stories: Nordost - A Story of Refinement
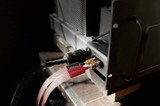
Time and exposure in the audiophile hobby teaches the listener that cables are simply an integral part of the refined HiFi experience. The practice of enjoying stereo music in high definition isn't new, but it took years of exploration and innovation to develop the modern understanding of the influence of cables in the art of high-end home audio.
As one of the leaders in cable technology in the last 30 years, Nordost has been one of the main drivers of this industry. They and others helped develop worldwide acceptance of cables as system components rather than simply "lengths of wire." Before this, previous generations of audio enthusiasts believed cabling did little to improve the sound of connected devices.
Despite the name and product labels, Nordost is not Scandinavian but rather an American cable brand with a long history of technical achievements and innovation in the audiophile cable field, and was founded by an audiophile named Joe Reynolds in Massachusetts in 1991. It has roots in an exciting period of the audiophile hobby, characterized by a reawakening of the desire for refinement after a power-hungry HiFi era where bigness and loudness ruled.
The story of audiophile cables begins in the early 1970s in Japan when an audiophile named Akihiko Kaneda began to write about the influence of the "skin effect" on the cable connection between amplifier and speakers. Skin effect is the tendency for electrical current to move toward the outer surface of a wire as the frequency of the signal rises. This can lead to eddy current fields within the cable, increased resistance due to current crowding, and also cause more of the energy to be influenced by the quality of the "dielectric," or cable jacket material. Different materials are known to store and release high-frequency energy in various ways based on their composition (i.e., their "capacitive" effects).
At the time, audio engineers understood the skin effect but largely believed it came into play in RF (radio frequencies) well above the audible spectrum and simply didn't matter for sound reproduction. We now know that the skin effect begins in large wire gauges quite early in the frequency range, and the modern audiophile use of heavy-gauge wiring brings this problem to the audio band more than ever before. Yet Kaneda's ears knew what the engineers of his time didn't, as its effect in his HiFi system was apparently and confoundingly audible.
Thanks to this observation of its sonic effect, Kaneda and a few other Japanese audiophiles carried out experiments in wire formation and geometry and reported on their results in the context of music playback through a high-end stereo system. The cable buzz was beginning.
Following the lead of the Japanese, French audiophile reviewer and speaker designer Jean Hiraga began his own studies into the benefits of "Litz wire," which was one of the construction methods being used by the Japanese to compensate for skin effect. Martin Colloms (HiFi journalist, co-founder of Monitor Audio and co-creator and publisher of HIFI Critic magazine) wrote and theorized further on the topic in 1977, which was said to inspire AudioQuest engineer Dave Gore to create a cable using a staggering 435 individually insulated wires, as the debut product from the now-well-known cable maker.
Litz construction (from the German word Litzendraht) uses many small wires that are individually enameled or insulated and then woven together, allowing their electrostatic and electromagnetic fields to have less interaction between the wires. Listeners to the Litz wire agreed on the high-frequency improvements, but opinions varied on the quality of bass using this approach.
Toward the late '70s, two notable commercial high-end audiophile speaker cables entered the market, one produced by Supra Cables (1976) in Japan and one from Fulton Musical Industries (1977) in America. Both offerings were not Litz, but instead large-gauge stranded wire, which attacked the skin effect using better dielectrics and a coating of silver on the wires to improve the high-frequency transmission.
Contrasting this with the common 18-gauge "lamp wire" that was used in so many audio systems at the time, the art of cable design was moving in the right direction. Large gauges on one side and Litz on the other, ideas were pouring in from all directions about how best to transmit the high-current signals between amplifiers and speakers.
In the 1980s, the audiophile hobby saw plenty of innovations in bigness, including high-wattage solid-state amplifiers with new 20-amp power connections known as the "muscle amps." Following suit and taking advantage of available power, extremely amplifier-taxing or just plain inefficient speakers were growing in number. With brands like Monster Cables experiencing exponential growth as well, the '80s audiophile quickly learned how to flex the power of sound.
As time went on, however, audiophiles slowly began to realize that "bigness" isn't everything in the hobby. In the 1990s, once the HiFi world had gotten that out of its system, changes began to appear in listening rooms and the marketplace alike. Listeners remembered that tube amplifiers used to sound really good. People started talking about their soundstages again. Because most tube amps could hardly awaken the KEF Reference products or drive B&W speakers with authority, speaker makers likewise began to develop more efficient and easier-to-drive options.
Not everyone was returning to tubes, but an appreciation of more Class A in the solid-state world tracked closely to the burgeoning SET (single-ended-triode) movement. After the "watts race" of the 1980s, there were now audiophile circles that turned their focus to low power, simple tube circuits driving higher-efficiency speakers.
For the solid-state listeners, speaker designers like Richard Vandersteen and John Dunlavy were showcasing the beauty of time-alignment, and David Wilson was seeing if he could recreate that bigness of the decade prior with more refinement. His unprecedented modular WAMM speaker system, for example, was a testament to these goals.
Refinements also occurred in the listening spaces, as an emphasis on surgical room treatment encouraged more unmolested sound waves to float effortlessly to grateful audiophile ears. Perspectives were changing, and so was the makeup of audio racks. All-new digital players and converters were in need of their own special cables, and connections were becoming more important than ever before.
Enter Nordost. Nordost was founded right when the audiophile hobby was awakening to this new period of refinement and reinvention. It was a great time to enter the scene, and the company immediately brought forward-thinking engineering to the American cable market.
Their first product, the "Flatline" speaker cable, caught national attention for its ability to uncover previously hidden details while its flat form factor allowed it to be run under the carpet and remain hidden. Audiophiles loved the cables, which were very well-reviewed, and Nordost's material innovations turned heads among cable manufacturers as well.
Flatline was the first audiophile cable to use a revolutionary DuPont material called FEP, which is a fluoropolymer plastic marketed under the brand name Teflon FEP when licensed from DuPont. It's similar to the more commonly known PTFE, but it's meltable, workable, transparent, and sunlight-resistant.
Nordost still uses a lot of FEP in its products today because it's a great-sounding dielectric (cable jacket material) with a low absorption rate. Scores of other cable companies have followed suit to employ FEP after Nordost did it in the '90s, and the material is found in cables all over the industry.
A few years after the Flatline, the introduction of the Nordost's new top-of-the-line SPM Reference cables completely captivated the audiophile cable conversation once again. Nordost's position in the industry was rising quickly in the "refinement" decade, and effusive reviews of the SPM left many audiophile tongues wagging, such as this reviewer from SoundStage! Network in 1997:
"It wasn't only 'ruthlessly revealing' wires that were beat-up on by SPM Reference. Other wires which definitely could not be called 'ruthlessly revealing' still sounded lame in comparison to SPM Reference."
The SPM Reference products, which included speaker and interconnect cables, also marked the beginning of Nordost's use of heavy silver plating on copper conductors. Silver is more conductive than copper, and its specific type of corrosion (or rather its "oxide" created from contact with air) is even more conductive than the silver on which it grows. But Nordost's implementation of silver wasn't only about conductivity.
A coating of silver also smoothes out the naturally-rough crystalline structure of the copper's surface, allowing higher frequencies easier flow once the skin effect comes into play. Add to this that silver's lattice structure is less prone to breakage and deformation than copper, and silver plating was one more piece of ammunition in the Nordost's war on the skin effect and other cable-caused issues. The technique is still employed in most of their cables to this day, prevalent in the Norse series and upward.
But perhaps the best innovations were yet to come. In 1999, Nordost introduced the Valhalla cable, and the world saw the first use of the proprietary "micro monofilament" (MMf) technology. This method was so ahead of its time that it's still employed today in many of Nordost's current products, from the Norse line all the way up to Odin Supreme Reference.
Nordost's breakthrough "micro monofilament" approach was a clever way to eliminate plastic as the dielectric (cable insulation), essentially putting a jacket on a wire without actually touching the wire. Well, almost without touching it. The "filament" describes a small string made of FEP wrapped in a spiral around the bare wire, resting inside an air tube made of FEP. The string touches the wire at one narrow point along the spiral to keep it centered in the tube, but it presents a minimal physical contact point in an otherwise inert air environment.
Air has the ideal electrical characteristics as an "insulator," meaning it won't allow energy to easily escape the cable. Allowing for more than 80% air contact with the bare wire is a very high-tech way to insulate it and curb energy loss. The Litz wire of the '70s and the monstrous cables of the '80s each had their own upsides, but neither could boast freedom from the plastic blanket like Nordost's MMf-equipped wires.
In Nordost's designs, the tubed wires are grouped together into different geometries and configurations. For speaker cables, Nordost arranges them side by side to create a flat ribbon, which achieves the best electrical properties for speakers and continues the classic flat look from the earlier years. Power cables and interconnects, however, would require different configurations based on the needs of the individual signals.
This technology was ahead of its time in 1999, and in the years since, alongside many other innovations, they've continued to update and refine MMf. Through extensive research and development, Nordost has been able to craft different types and levels of musical experience into different lines and models of cable using the same guiding philosophies throughout. By adjusting the conductors, changing the gauges, or adjusting the groupings of the tubes, they're able to adjust the electrical characteristics of each cable while keeping the overall design philosophy intact.
Doubled conductors inside the FEP tubes of Frey and Tyr interconnects, for example, can provide upgrades in low frequency and dynamics over the single-stranded Heimdall, but the three can be mixed and matched in a system without any sonic confusion or loss of associated synergy.
With the 20th Century in the rearview, Nordost stretched into the world of Ultra-Fi, bringing much innovation and their reputation for stunning resolution to the scene. The HiFi audio world gasped when the Odin Supreme Reference cables, and their sweat-inducing prices, were introduced. Odin showcased all of the modern techniques Nordost had been busy developing. Advanced geometries, advanced shielding, mechanically tuned tensioning, and state-of-the-art connectors were implemented along with other proprietary treatments.
More recently, in its constant cycle of refinement, Nordost's updates to the Valhalla using techniques from the Odin line prompted some to consider the updated Valhalla 2 cables as sonically nipping at the heels of Odin (a strange image, given the mythology) in performance. Eventually, in 2017, Nordost's new Odin 2 cables were introduced with even more new innovations, once again restoring the balance of power in the Nordost lineup.
According to Jacob Heilbrunn in The Absolute Sound's 2017 review, "The more I listened to the Odin 2, the faster it became apparent that it greatly exceeds its predecessor in every parameter of performance."
Among other improvements, the in-house-made HOLO:PLUG was rolled out for the Odin 2, which solved a classic cable maker's dilemma. State-of-the-art plugs and connectors often come from OEM plug manufacturers, and the best-sounding ones were still not designed with Nordost's unique cable geometries in mind. The natural next step for Nordost was to make their own.
The HOLO:PLUG's wire sockets are precisely angled and specifically designed to mate with Nordost cable layout, allowing machine termination for better precision without ruining the geometry and undercutting the design benefits.
Throughout the years since its debut, Nordost has shown the audiophile world that the path to success begins in the laboratory and is backed by real science. From the beloved Flatline cables to the space-age MMf technology, Nordost's constant invention, consistent revision, and unrelenting march toward excellence are what it took to achieve the status as a worldwide leader in the audiophile cable market.
Since the departure from "lamp wire" all those years ago, audiophiles have thoroughly embraced the fact that cables are an integral component in any well-designed system rather than just a length of wire. With many great options available in the modern marketplace, Nordost's goals of linearity and purity, along with products that simply over-deliver on their promises, make them a true story of refinement.
Nordost encourages its dealers to prove the products' worth by offering generous trial periods with all of its cables. The Music Room goes further than most, extending this period to 60 days and guaranteeing a great mate with any system. Take a look at the lineup of Nordost cables below, and take the plunge, knowing you can go a different direction if it's not working for you.
Nordost, a story of refinement, is one audiophile company that promises to keep the audiophile world on seat-edge to see what they come up with next.